Elysium has developed an advanced functionality to model piping and structures from 3D laser scanned point clouds into Autodesk Revit. The new capability is part of the latest release of Elysium’s point cloud utilization software, InfiPoints, available now.
The new plug-in allows Revit users to reduce their modeling time dramatically, with benefits such as:
- Not having to create models of existing facilities from scratch
- The ability to import CAD data automatically extracted from point cloud data with InfiPoints into Revit to add finishing touches
- Adding standard pipe specifications in InfiPoints that can be carried over into Revit
Industry pioneers and service providers have recently begun employing 3D laser scanners to capture the on-site environment more thoroughly, accurately, and efficiently. Modeling from the environment without the right point cloud software, however, can be labor-intensive and time-consuming.
InfiPoints can automatically extract pipes and planes from point cloud data captured from 3D laser scanners. Users can then create CAD models with a few simple mouse operations.
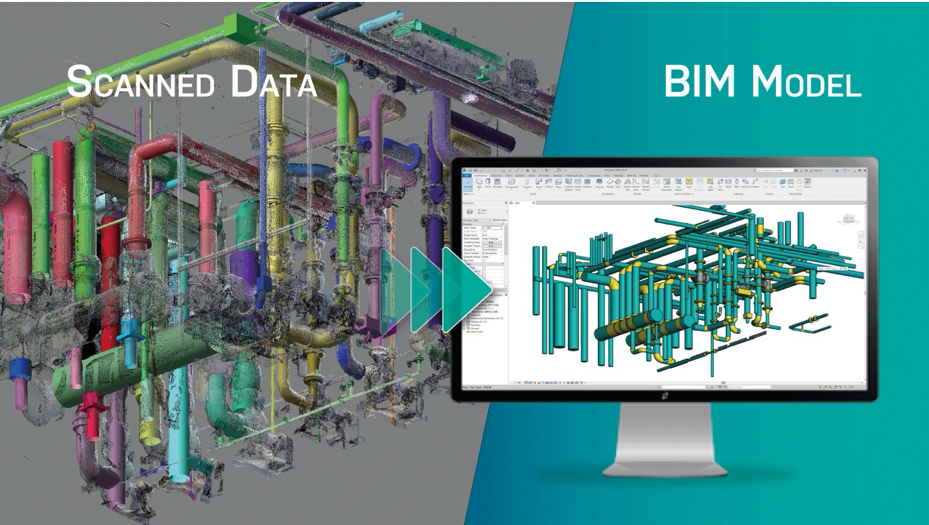
The InfiPoints Revit Plug-in enables the direct connection of this advanced point cloud solution to Revit users. InfiPoints exports the CAD geometry extracted from the point cloud parametrically, which allows flexible editing of the extracted model. Non-geometrical information such as piping standards and attributes are also delivered to Revit, adding value to communication with contractors for maintenance and construction.
“Revit has been a de facto standard BIM software throughout the world,” states Atsuto Soma, CTO of Elysium. “We believe that this newest feature will spur greater adoption of Elysium’s 3D data utilization technology to BIM modelers globally and contribute to streamlining workflows in the MEP industry.”
What is InfiPoints?
InfiPoints is an all-encompassing point cloud utilization software that goes beyond 3D visualization of laser-scanned 3D point cloud data. InfiPoints covers the entire point cloud utilization workflow in five steps consisting of data import, data pre-processing, 3D analysis, 3D modeling, and the creation of various outputs.
Data Import
The first step after capturing the environment through 3D laser scanning is importing the point cloud data into the software. InfiPoints can import hundreds of scans, billions of points, and supports several scan data formats from .e57, .fls, .zfs, .ptx, and more to fulfill needs from a variety of hardware users.
Data Pre-processing
The second step is to register the scanned data. InfiPoints supports automatic marker and markerless registration for smooth processing to visualize multiple scans. For further visualization perfection, InfiPoints also has a powerful noise reduction capability not only to remove floating noise but to also remove overlapping noise resulting from different capture views on the same object and reflections.
3D Analysis
Import CAD/BIM to validate between point clouds and models, and see the deviations with a color map. Real-time collision detection and analysis will display how to best move equipment in and out of an area. Create paths for equipment to show the best route and even share it through a videoThe third step is to utilize and analyze the point cloud data that is captured for engineering purposes. InfiPoints can easily measure, validate, and perform collision detection within the 3D environment. Extraction of planes and cylinders enables a precise measurement within the point cloud world. Utilizing the center lines of pipes and extracted planes, InfiPoints provides more accurate measurements compared to measuring from individual points.
3D Modeling
One of the major highlights of InfiPoints is the dynamic modeling capability to automatically extract features, such as pipes, ducts, and steel structures, and streamline the conversion to 3D CAD and BIM models.. Quickly go from point cloud to BIM for all of your downstream needs. This capability is widely used in MEP and plant engineering industries for use cases such as piping construction and equipment maintenance simulation.
Output Creation
Sharing Point Cloud Data One of the most critical aspects of 3D scanned data is the ability to share the information. InfiPoints has a multitude of output formats for a variety of uses and needs. Output directly to Revit with the InfiPoints Revit Plugin. Export a neutral CAD file, such as IGES, STEP, Parasolid, or a native CAD format to be used in SOLIDWORKS, Siemens NX, CATIA, Autodesk Inventor, or PTC Creo.
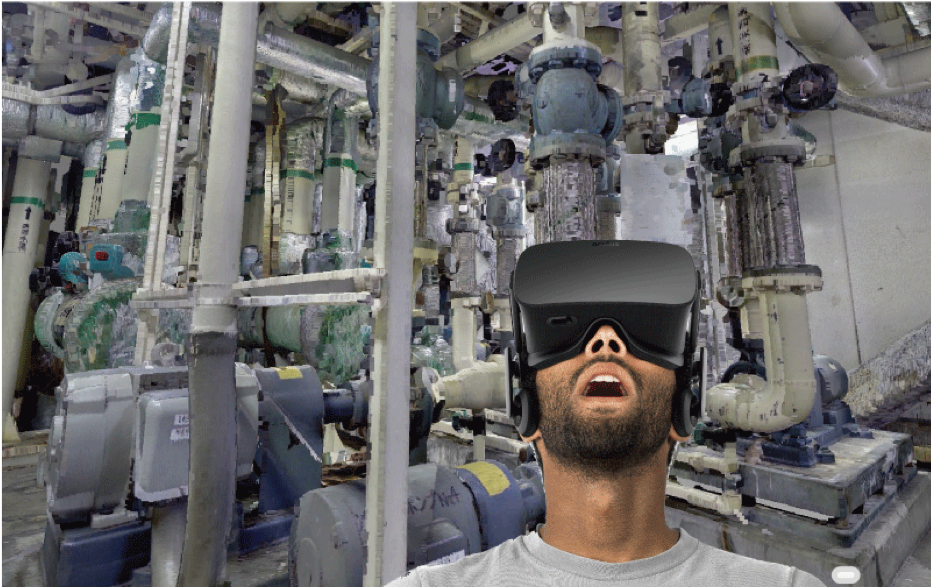
InfiPoints can export a standalone viewer file that provides additional functionality to measure and analyze the point cloud data without licensing or software download. You can even become immersed inside the point clouds with InfiPoints VR through Oculus Rift or HTC Vive.
InfiPoints Case Studies
MEP & Plant Maintenance
InfiPoints has become a powerful tool for MEP and Plant Maintenance for the use in retrofitting and maintenance in areas with many piping runs and industrial equipment. Automatic extraction of pipes and planes from point clouds and connecting it with CAD and BIM has helped these industries utilize point cloud data more effectively. For some cases, MEP and plant maintenance have seen a reduction of 50% in modeling time.
Civil Engineering
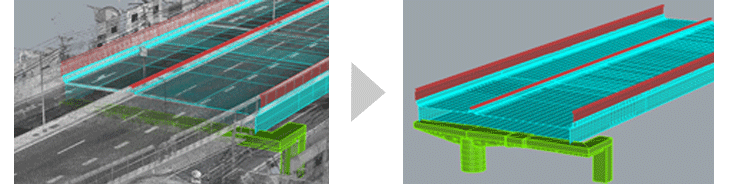
Point cloud utilization is not limited to industrial sites and plants. InfiPoints’ technologies are utilized in civil engineering use cases for highway maintenance and analysis, as well. Mobile Mapping Systems (MMS) are used for scanning large-scale highway systems over 300km.
Digital Archiving
Point cloud is not just for engineering, but also valuable for visualization. From heritage sites, museums, and even for disaster aftermath, InfiPoints can pre-process and prepare point clouds for viewing not only in a computer screen, but with VR to trigger an immersive experience.